
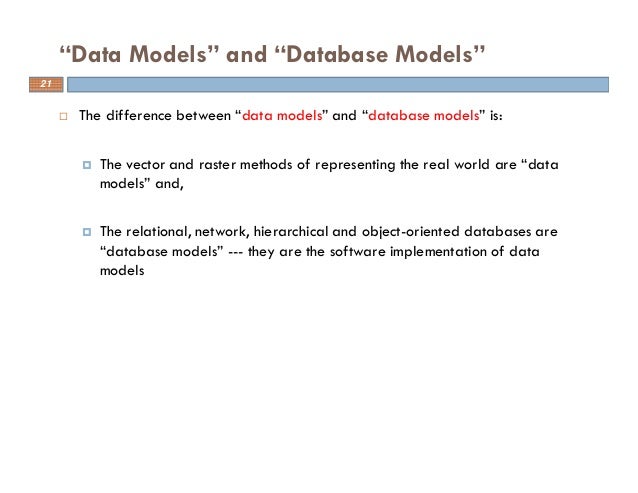
For example, low cost doesn’t normally go hand in hand with high quality. Does the company intend to be a low-cost producer and to compete on the basis of price? Or does it plan to focus on quality and go after the high end of the market? Many decisions involve trade-offs. Before making decisions about the operations process, managers must consider the goals set by marketing managers. The decisions made in the planning stage have long-range implications and are crucial to a firm’s success. Let’s take a closer look at each of these responsibilities. The operations manager is directly involved in efforts to ensure that goods are produced according to specifications and that quality standards are maintained. At this stage, they also oversee the purchasing of raw materials and the handling of inventories. They must solicit and respond to feedback and make adjustments where needed. Once the production process is under way, managers must continually schedule and monitor the activities that make up that process. During production planning, managers determine how goods will be produced, where production will take place, and how manufacturing facilities will be laid out. Their responsibilities can be grouped as follows: Making the decisions involved in the effort to attain these goals is another job of operations managers. They must fine-tune their production processes to focus on quality, to hold down the costs of materials and labor, and to eliminate all costs that add no value to the finished product. To perform this function in today’s business environment, manufacturers must continually strive to improve operational efficiency.
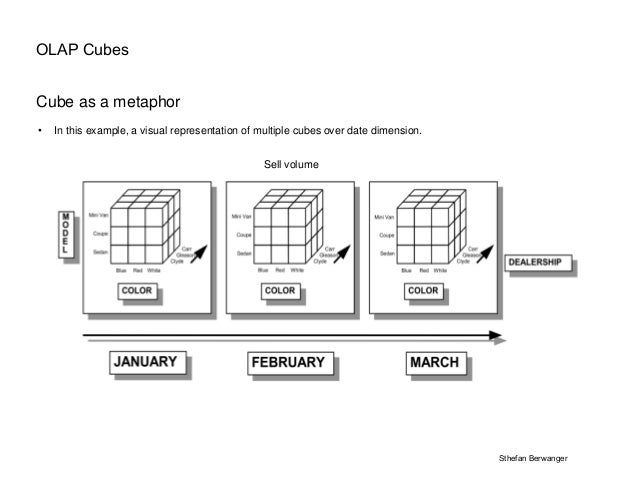
Like PowerSki, all manufacturers set out to perform the same basic function: to transform resources into finished goods. Figure 10.2 illustrates these traditional functions of operations management. In other words, operations managers manage the process that transforms inputs into outputs. In addition, operations managers are involved in planning and controlling the systems that produce goods and services. The job of operations management (OM) consists of all the activities involved in transforming a product idea into a finished product. The upper-level manager who directs this transformation process is called an operations manager. Thus, to compete with other organizations, a company must convert resources (materials, labor, money, information) into goods or services as efficiently as possible. Like PowerSki, every organization-whether it produces goods or provides services- sees Job 1 as furnishing customers with quality products.
#BASIC DATA TYPES AND OPERATIONS TV#
It was showered with honors, including Time magazine’s “Best Invention of the Year” award.1 Stories about the Jetboard appeared in more than fifty magazines around the world, and it was featured in several movies, over twenty-five TV shows, and on YouTube.2 It was worth it, though: the Jetboard was an exciting, engine-propelled personal watercraft – a cross between a high-performance surfboard and a competition water-ski/wakeboard that received extensive media attention and rave reviews. It took sixteen years for Bob Montgomery and others at his company to develop the PowerSki Jetboard, and this involved thousands of design changes. The product development process can be complex and lengthy. Watch the videos that demonstrate what the Jetboard can do. To see it in action, visit the company’s Web site at.
